Vacuum systems
The vacuum system is an inherent part of your deodorizing system. It is important for both, final product quality of the deodorized product and for the overall operating costs of the deodorizing section.
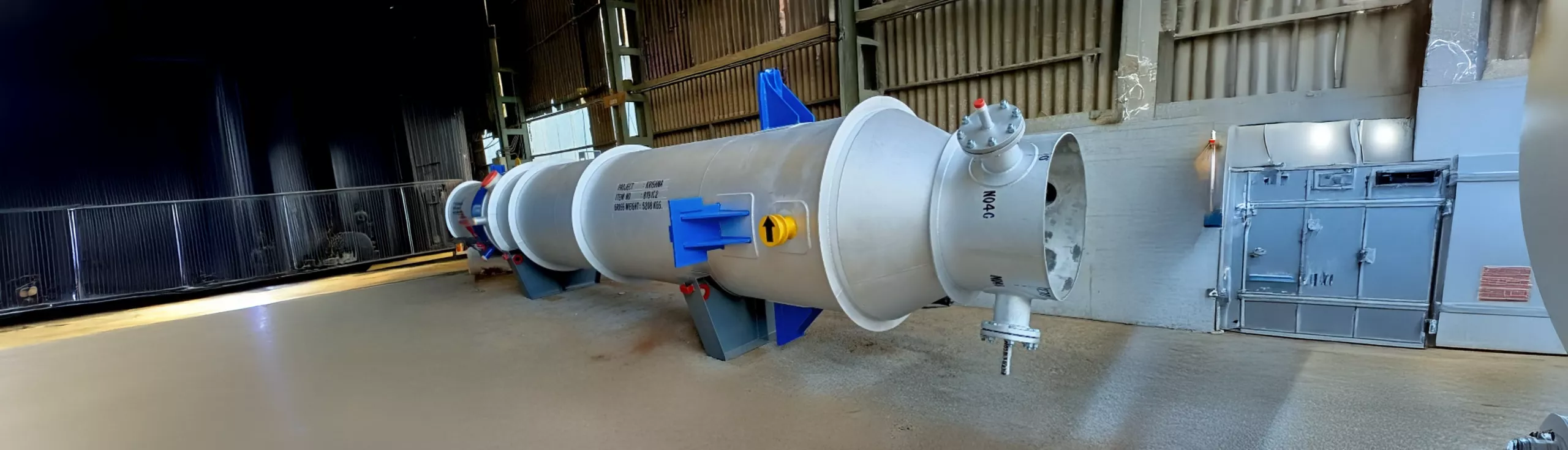
Desmet carefully designs the vacuum system based on the operating parameters of the deodorizing section. Different vacuum systems can be considered depending on capacity and overall requirements of the deodorizing section, but nowadays mainly two types of vacuum systems are installed in modern refineries:
- Closed chilled barometric vacuum system
- Dry ice condensing system (‘Sublimax’ system)
These systems are preferred because of the much lower operating costs (steam and/or electricity) and environmental advantages (less smell, less effluents) compared to more traditional vacuum systems.
Desmet has developed his proprietary designed Sublimax ice condensing system, that has a lot of benefits especially for higher capacity plants (>300 tpd). The operating principles of the Sublimax system are explained below.
How does it work
The operation of the Sublimax ice condensing system is fully automated and the operation is very reliable.
The vapours coming from the deodorizer scrubber system, are condensed at very low temperature (<-25°C) on the large tubes of the Sublimax 2G Ice condensers. This means that only the uncondensable gasses need to be sucked by the vacuum unit at the outlet of the condensers. This results in much less overall electricity and steam consumption of the vacuum system.
The proprietary vertical design of the Sublimax ice condensers also allows to melt down the iced vapours with hot water circulation, which allows additional steam savings.
The Sublimax ice condensers exist in different standard capacities to cover the whole capacity range of the deodorizing section. In most of the cases the section contains 2 or 3 condensers that operate alternate in fully automated cycle times.
The chilling systems used to generate the low temperatures in the condensers are mostly based on ammonia as the preferred refrigerant. However, recently Desmet also has developed a system with CO2 as the refrigerant – ‘Sublimax Safe’ – in case the use of ammonia is restricted (e.g. refineries in urban locations, stringent legislation).
Finally, the steam consumption can be minimized by the use of electrical vacuum pumps sets instead of more classical vacuum booster sets.
Key advantages